Środki rozdzielające
Jesteśmy światowym liderem w produkcji innowacyjnych środków rozdzielających.
Środki rozdzielające (substancje rozdzielające w przypadku technologii odlewania ciśnieniowego) stanowią integralną część wielu procesów produkcyjnych. Specjalistyczne środki rozdzielające mogą zwiększać produktywność, wydłużać żywotność narzędzi, form odlewniczych i wtryskowych, skracać czas cyklu, poprawiać jakość wykonanych elementów oraz zmniejszać odsetek odpadów i defektów. To tylko niektóre z wielu możliwych i dostępnych korzyści.
Współpracujemy ściśle z zespołem klienta w celu wspólnego doboru idealnego środka rozdzielającego, gwarantującego usprawnienie procesów technologicznych danego klienta.
Konwencjonalne środki rozdzielające (substancje rozdzielające)
Oferujemy szerokie portfolio produktów konwencjonalnych (tzn. środków rozdzielających aplikowanych w każdym cyklu). Nasze konwencjonalne środki rozdzielające do form zapewniają następujące zalety:
- Są dostępne w wersjach wodnorozpuszczalnych i rozpuszczalnikowych.
- W zależności od zastosowania są dostępne w postaci gotowej do użycia lub przeznaczonej do rozcieńczenia.
- Są przystosowane do wielu typów urządzeń natryskowych.
- Umożliwiają dostosowanie stężenia do danej aplikacji oraz parametrów płynięcia.
- Doskonale nadają się do stosowania w produkcji elementów formowanych o bardzo skomplikowanej geometrii.
- Minimalizują powstawanie osadów i skorup wewnątrz form.
Półtrwałe środki rozdzielające (substancje rozdzielające)
Stosowane dziś, zaawansowane, półtrwałe, wodnorozpuszczalne lub rozpuszczalnikowe środki rozdzielające do form oferują wiele potencjalnych korzyści. Technologia półtrwałych środków rozdzielających to przemysłowa alternatywa do tradycyjnych środków rozdzielających o ogromnym zużyciu, nakładanych przez firmy produkcyjne techniką natryskową lub nakładanych w przed każdym cyklem produkcyjnym. Zalety dla naszych klientów:
- Większa liczba rozformowań w porównaniu z typowym środkami rozdzielającymi.
- Większa liczba cykli odlewania na zmianę roboczą.
- Mała ilość środka na każdą aplikację sprzyja utrzymaniu miejsca pracy w czystości i umożliwia zmniejszenie nakładów magazynowych.
- Zmniejszenie ilości odpadów.
- Znacznie wyższa żywotność form dzięki własnościom ochronnym.
- Przydatność do produkcji złożonych elementów formowanych/struktur dzięki precyzyjnemu i łatwemu nakładaniu środka rozdzielającego.
- Stabilny wygląd formowanych elementów.
Środki rozdzielające (substancje rozdzielające) bez silikonu
Firma Chem-Trend oferuje bardzo szeroką paletę innowacyjnych i zrównoważonych środków rozdzielających, nie zawierających silikonu. Środki rozdzielające bez silikonu mają wiele zalet:
- Zmniejszą ilość tłustych pozostałości i ułatwiają malowanie i powlekanie po wyjęciu z formy.
- Zmniejszą ryzyko zanieczyszczenia i eliminują kosztowne operacje procesów produkcyjnych.
- Zwiększają produktywność i zmniejszają koszty operacyjne.
Dlaczego warto wybrać środki rozdzielające firmy Chem-Trend?
Realne korzyści
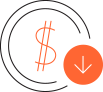
Naszym celem jest tworzenie wartości dodanej dla naszych klientów. Nasza wyróżniająca się w branży oferta środków rozdzielających obejmuje wodnorozpuszczalne i rozpuszczalnikowe produkty oraz środki zawierające i niezawierające silikon w wersjach półtrwałych lub konwencjonalnych. Nasza oferta obejmuje właściwe produkty, umożliwiające optymalizację codziennych operacji technologicznych. Nasze rozwiązania zapewniają rozwiązanie kosztownych problemów produkcyjnych oraz zwiększają wydajność produkcji i jakość produktu dzięki najwyższym parametrom środków rozdzielających.
Maksymalna wydajność produkcyjna
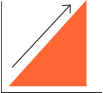
Firma Chem-Trend szeroki zakres różnych środków rozdzielających. Są one dostosowane do konkretnych potrzeb i umożliwiają uzyskiwanie maksymalnych wyników. Każdy proces formowania jest w jakiś sposób wyjątkowy. Optymalne rozformowanie wymaga zastosowania unikalnych rozwiązań. Zespół naszych ekspertów w praktyczny i realny sposób ocenia wraz z klientem stosowane procesy technologiczne i określa możliwości optymalizacji we wszystkich obszarach. W kolejnym etapie, nasz zespół badawczo-rozwojowy projektuje indywidualne rozwiązania dla działalności danego klienta.
Realny, zrównoważony rozwój

Wielu spośród naszych klientów usilnie pracuje nad poprawą zrównoważonego charakteru swoich przedsiębiorstw. Oferta firmy Chem-Trend cieszy się niezwykłym powodzeniem także dlatego, że od początku naszej działalności koncentrujemy się na zmniejszaniu oddziaływania naszych produktów na środowisko naturalne. Już w latach 60-tych uprzedniego stulecia opracowaliśmy i wypuściliśmy na rynek pierwszy, wodnorozpuszczalny środek rozdzielający. Miał on bardzo pozytywny wpływ na ochronę zdrowia i bezpieczeństwo pracy wtryskarek wysokociśnieniowych, ponieważ w odróżnieniu od stosowanych wtedy środków rozdzielających do form, nie posiadał w swoim składzie ani grafitu, ani rozpuszczalników. Dużą część naszych starań poświęcamy eliminowaniu czynników szkodliwych dla środowiska naturalnego, takich jak stosowanie lotnych związków organicznych (Volatile Organic Compounds, VOS) w rozpuszczalnikowych środkach rozdzielających. Obecnie firma Chem-Trend w całej branży wyróżnia się innowacyjnością stosowanych rozwiązań.
Znajdź środek rozdzielający przy pomocy naszej wyszukiwarki lub skontaktuj się z nami.
WIADOMOŚCI
POWIĄZANE MYŚLENIE
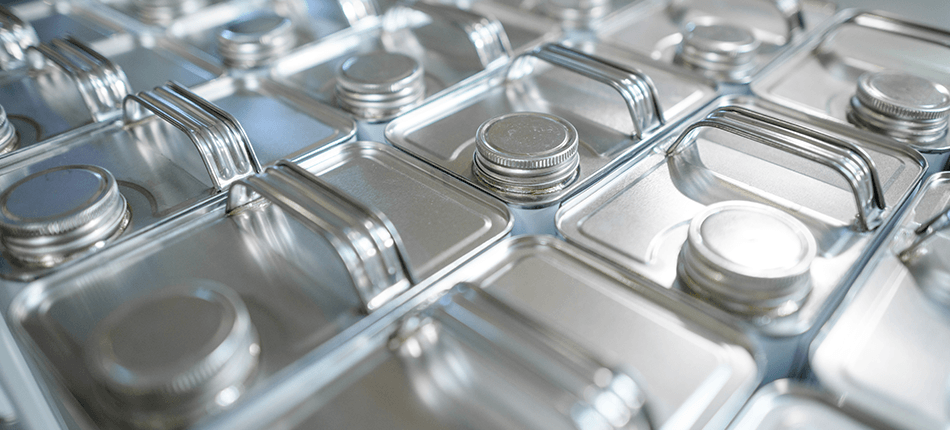
Środki rozdzielające: Przyczepność powłok i zastosowanie antystatycznych produktów uzupełniających.
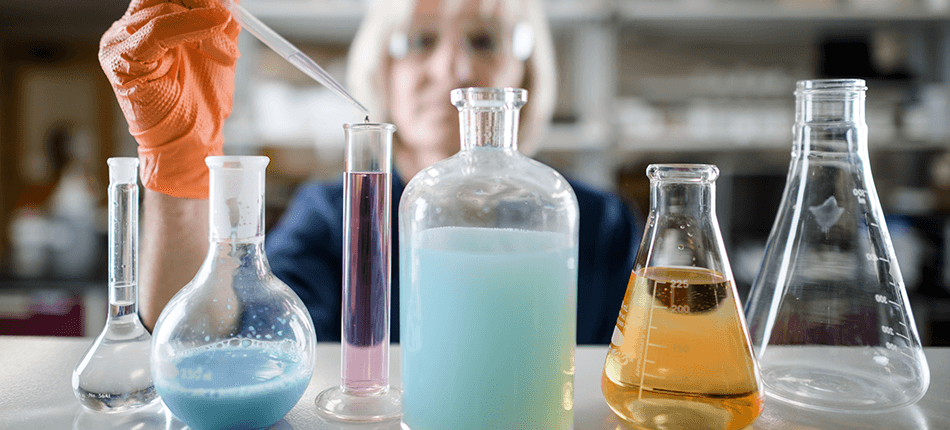
Innowacyjne trendy w dziedzinie środków smarnych do matryc dla ciągle zmieniających się wymagań dotyczących wydajności i procesów technologicznych.
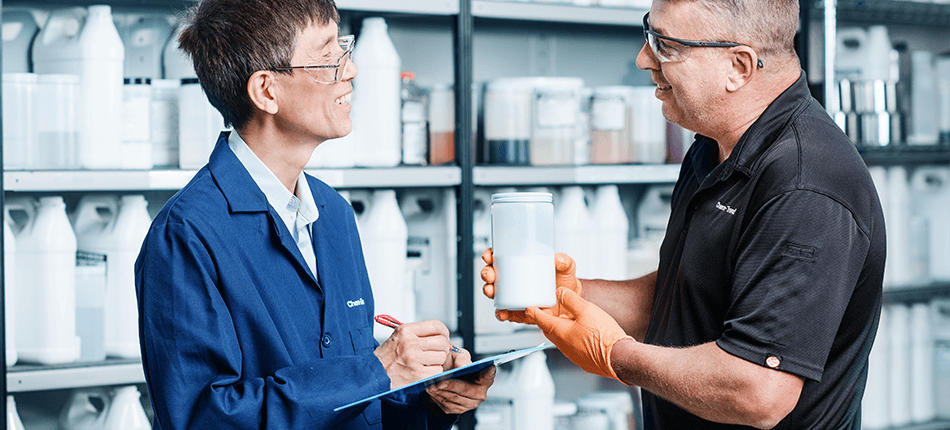
Technologia i trendy w dziedzinie środków rozdzielających i środków smarnych do odlewania aluminium.
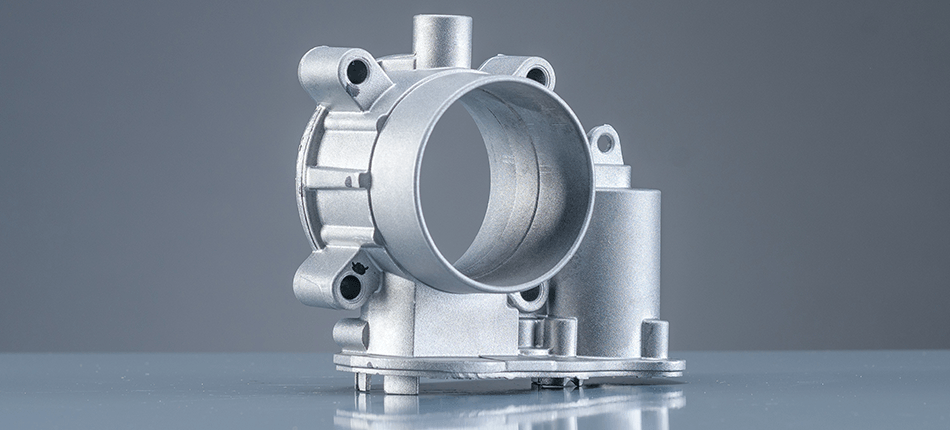
Technologia i trendy w zakresie środków rozdzielających do form i smarów do odlewania stopów magnezu.
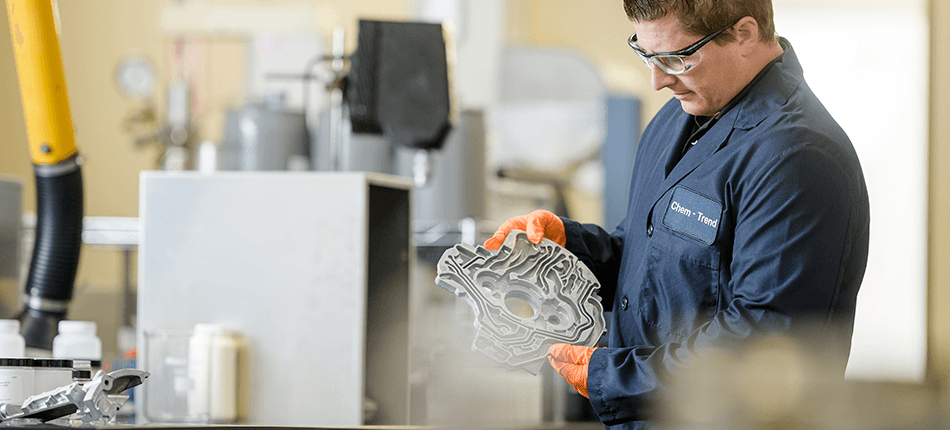
Innowacyjne technologie środków rozdzielających do formowania wtryskowego (formowania)
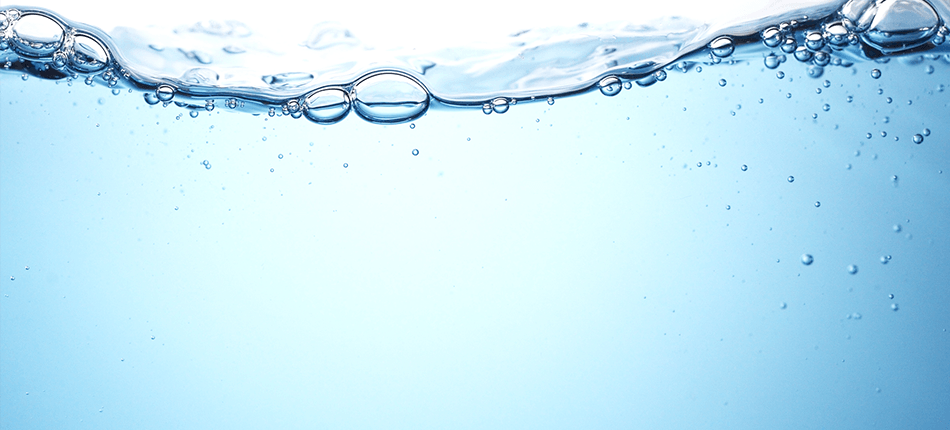
Redukcja zużycia wody dzięki zastosowaniu zaawansowanych technologicznie środków smarnych do matryc.
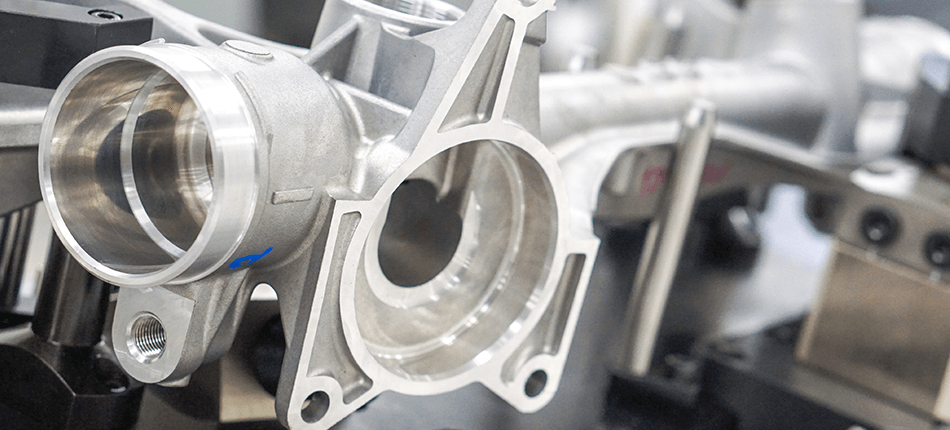
Wpływ środków rozdzielających stosowanych w odlewnictwie ciśnieniowym na równowagę cieplną form
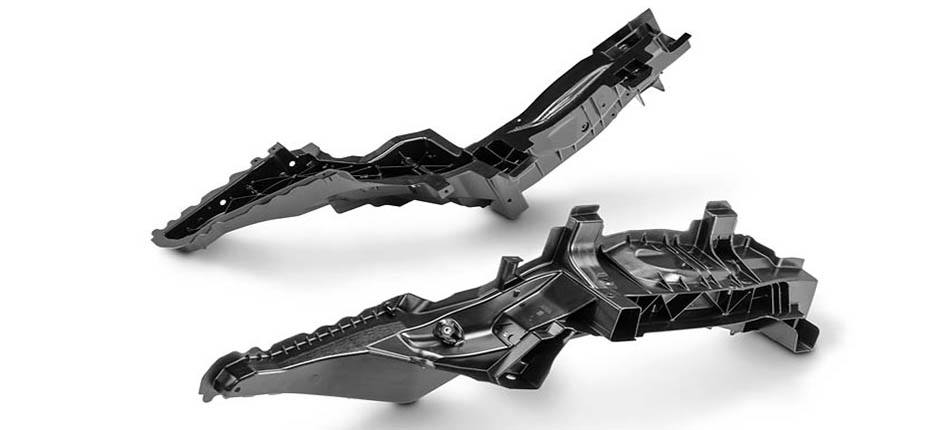
Odpowiedni środek rozdzielający – większa wydajność i zrównoważony rozwój
BROSZURY
Środki rozdzielające (Środki antyadhezyjne) Lusin®
Środki rozdzielające Chem-Trend Lusin® zostały stworzone, aby wspierać przemysł przetwórstwa tworzyw sztucznych dzięki swoim właściwościom zapobiegającym przywieraniu oraz poprawianiu produktywności, jakości i żywotności narzędzi.
Katalog produktów do obsługi form Lusin® i środków rozdzielających firmy Chem-Trend
Kompletne rozwiązanie dla większej wydajności
Nasze rozwiązania w zakresie produktów do obsługi form i środków antyadhezyjnych zapewniają najlepsze możliwe wsparcie w celu zwiększenia wydajności i zmniejszenia kosztów procesu produkcyjnego. Jako kompletny system nasze produkty do obsługi form Lusin® doskonale się uzupełniają i przynoszą wiele korzyści. Regularne zabiegi konserwacyjne z użyciem naszych środków czyszczących do form i odtłuszczaczy Lusin®, środków ochronnych do form i środków smarnych zapewniają najlepszą możliwą pielęgnację i konserwację narzędzi.
Często zadawanych pytaniach: Środki oddzielające dla przetwórstwa tworzyw sztucznych
Jakie są zalety i wady bezsilikonowych środków rozdzielających w porównaniu ze środkami zawierającymi silikon? Dowiedz się więcej w naszym dziale FAQ.
HERA™, środek rozdzielający do form do odlewania ciśnieniowego
Środki HERA™ mają wiele zastosowań: od standardowych i wysoce plastycznych mieszanek specjalnych aż po skomplikowane geometrie elementów, oraz obejmują szeroki zakres temperatur form.
Środki rozdzielające HERA™-Light są odpowiednie do wszystkich metod aplikacji stosowanych w odlewnictwie ciśnieniowym.
Środek rozdzielający HERA™-Light charakteryzuje się dobrą przyczepnością warstwy środka rozdzielającego w szerokim zakresie temperatur form. Obciążenie termiczne narzędzia natryskowego jest bardzo niskie, następuje szybkie wytworzenie warstwy.
Więcej dowiesz się z naszej ulotki.
Środki rozdzielające Chem-Trend® SL-6XXXX do odlewania ciśnieniowego wspomagają też kolejne procesy technologiczne przetwórstwa materiałów
Odlewy ciśnieniowe produkowane z użyciem środków Chem-Trend® SL-6XXXX są kompatybilne z metoda malowania kataforetycznego. Możliwe jest również ich spawanie.
Więcej dowiesz się z naszej ulotki.
FAQ
Zależy ona w znacznym stopniu od wymagań przemysłu i procesów. W niektórych branżach produkty na bazie rozpuszczalników nie mogą być już stosowane z powodów bezpieczeństwa i higieny pracy lub obowiązujących przepisów. Na przykład w odlewnictwie ciśnieniowym, produkcji opon oraz ogólnie w przemyśle gumowym stosowane są głównie środki na bazie wody. Przemysł poliuretanowy wykorzystuje zarówno środki rozdzielające na bazie wody, jak i rozpuszczalników, z kolei w produkcji materiałów kompozytowych i termoplastycznych obecnie stosuje się głównie środki rozpuszczalnikowe.
Produkty na bazie wody są bardziej wrażliwe na błędy w stosowaniu (pojawiają się problemy z odpowiednim zwilżeniem form) oraz wolniej odparowują (na co można wpływać sposobem aplikacji, warunkami procesu oraz poziomem wilgotności w otoczeniu), niż produkty rozpuszczalnikowe.
Produkty wodne są bardziej podatne na reakcje chemiczne między wodą pozostającą na powierzchni formy a formowanym materiałem (np. podczas formowania poliuretanów może powstawać mocznik).
Ta kategoria środków rozdzielających wymaga również zastosowania bardziej zaawansowanych środków technicznych, aby zapewnić ich stabilną emulgację oraz odporność na aktywność biologiczną. Aby środki rozdzielające na bazie wody mogły być szerzej stosowane w większej ilości branż, należy znaleźć odpowiedź na te wyzwania.
W przypadku produktów aplikowanych inaczej niż z puszki aerozolowej, preferuje się stosowanie wysokiej jakości pistoletów natryskowych lub instalacji natryskowych sterowanych czasowo.
Metodologia stosowania zależy od wyboru nośnika, składu samego środka rozdzielającego oraz procesu i jego otoczenia. Podstawowym czynnikiem, na który należy zwrócić uwagę, jest aplikacja, która istotnie wpływa na wydajność środka rozdzielającego. W większości przypadków środki rozdzielające są aplikowane pistoletem natryskowym, który jest obsługiwany ręcznie lub przez robota. W niektórych zastosowaniach wykorzystywane są programowalne systemy natryskowe z wieloma dyszami, które umożliwiają stosowanie jednego lub więcej środków rozdzielających. Rozmiar dysz jest regulowany, co umożliwia odpowiednie rozpylanie (zależne od oczekiwanej wydajności i lepkości środka rozdzielającego) oraz odpowiednie zwilżanie powierzchni. Aplikacja metodą natrysku może być wspomagana pneumatycznie (gdy powietrze jest wykorzystywane do rozbijania i rozpylania kropel) albo wykorzystywać proces „airless” (gdy atomizacja jest uzyskiwana przez dyszę pracującą pod odpowiednio wysokim ciśnieniem). Do aplikacji środków rozdzielających w postaci proszku lub cieczy mogą być też stosowane pistolety elektrostatyczne. W niektórych zastosowaniach środki rozdzielające mogą być też aplikowane z puszek aerozolowych, albo nawet metodą nacierania zautomatyzowanego lub ręcznego.
Każdy typ środka ma swoje specyficzne zalety (+) i ograniczenia (–).
Oto ich krótki przegląd:
Rozpuszczalnikowe środki rozdzielające:
+ Łatwiejsza aplikacja. Baza rozpuszczalnikowa ułatwiająca zwilżanie powierzchni. Zależnie od kompozycji rozpuszczalników można sterować szybkością odparowania. Wybrany rozpuszczalnik może ułatwić rozpuszczanie / dyspersje aktywnych składników środka rozdzielającego.
– Niezbyt przyjazne środowisku. Większe problemy z ochroną zdrowia (lotne związki organiczne) i bezpieczeństwem (ryzyko pożaru), niż w przypadku produktów nierozpuszczalnikowych.
Wodne środki rozdzielające:
+ Przyjazne środowisku, nie stanowią ryzyka pożarowego. Mogą czasami być rozcieńczane (są wówczas dostarczane w formie koncentratu). Mogą być w razie potrzeby używane do schładzania form. Stosowane technologie pozwalają uzyskać skuteczność rozdzielania porównywalną z rozpuszczalnikowymi środkami rozdzielającymi.
– Wymagają bardziej skomplikowanej technologii produkcji. Trudniej uzyskać jest równomierne zwilżenie form. Ten rodzaj środków rozdzielających jest bardziej podatny na problemy ze stabilnością oraz ryzyka biologiczne. Środki rozdzielające na bazie wody parują wolniej, niż ich konkurenci na bazie rozpuszczalników, i mogą być nieodpowiednie w przypadku procesów formowania w określonych temperaturach otoczenia, lub procesów o krótkim czasie cyklów. Woda pozostająca na formie może wpływać na jej wydajność (uwięziona para), albo nawet reagować chemicznie z formowanym materiałem. Jest to szczególnym wyzwaniem w przypadku formowania elementów z poliuretanu.
Środki rozdzielające bez nośnika:
+ Mogą być stosowane w gotowej postaci dzięki nieobecności nośnika. Brak parowania. Zaobserwowano mniejszy hałas podczas aplikacji. Nie wymagają rozpuszczania ani zbiorników do przechowywania. Brak ciekłych odpadów.
– Ryzyko pylenia w przypadku nieodpowiedniej aplikacji. Potrzebne są specjalne narzędzia do aplikacji (często są to elektrostatyczne pistolety natryskowe), które wymagają dużych inwestycji. Stosowanie środków rozdzielających pozbawionych nośnika może wymagać również dodatkowej modyfikacji narzędzi formujących, aby zagwarantować ich odpowiednią temperaturę. Czynniki te często ograniczają przydatność tej kategorii środków rozdzielających.
Środki rozdzielające działające rozpuszczające częściowo powierzchnię produkowanych elementów
+ Łatwa aplikacja. Mniej zaawansowana technologia aplikacji i większa tolerancja podczas pracy (nawet w przypadku mniej doświadczonych operatorów).
– Tendencja do gromadzenia się w formie w przypadku nadmiernego dozowania. Zasadniczo warstwa rozdzielająca częściowo przechodzi na formowany element, co może mieć negatywny wpływ na późniejsze etapy produkcji (malowanie, klejenie itp.) w przypadku zastosowania nadmiernej ilości, lub jeżeli substancje chemiczne wchodzące w skład środka rozdzielającego są niekompatybilne z dalszymi etapami procesu. Jeżeli środki te są na bazie wody, mogą one schładzać formę, usuwając z systemu ciepło / energię (co może być wadą, jeżeli nie zostało to uwzględnione w procesie).
Półtrwałe środki rozdzielające:
+ Wymagają znacznie niższej częstotliwości aplikacji niż rozpuszczające środki rozdzielające, ponieważ warstwa środka rozdzielającego utrzymuje się przez kilka cykli formowania (zależnie od warunków procesu). Wpływają korzystnie na stabilność i ciągłość procesu produkcji, ponieważ zmniejsza się ilość przerw potrzebnych do stosowania środka rozdzielającego. Jedynie bardzo mała ilość środka przechodzi na formowaną część, co ułatwia dalsze kroki pracy (powlekanie, klejenie). Środek rozdzielający można aplikować regularnie na formę, odświeżając jego warstwę. Ta kategoria środków rozdzielających pozwala uzyskać doskonałe połączenie właściwości chemicznych i fizycznych, zapobiegające gromadzeniu się osadów i gwarantujące uzyskanie wymaganej wydajności rozdzielania.
– Wymaga lepszego szkolenia operatorów, ponieważ konieczne jest przestrzeganie prawidłowej częstotliwości odświeżania warstwy rozdzielającej. Formy muszą być czyste, aby umożliwić prawidłową interakcję między środkiem rozdzielającym a powierzchnią formy podczas pierwszej aplikacji środka rozdzielającego.
Wewnętrzne środki rozdzielające do form:
+ Ograniczają konieczność stosowania zewnętrznych środków rozdzielających.
– Mogą stopniowo dostawać się na powierzchnię, wpływając negatywnie na dalsze procesy obróbki (powlekanie, klejenie) lub wygląd części. Często nie eliminują konieczności zastosowania zewnętrznych środków rozdzielających, ponieważ wewnętrzne środki rozdzielające nie zawsze migrują na powierzchnię formy lub nie gwarantują stuprocentowej skuteczności rozdzielania. Wewnętrzne środki rozdzielające nie charakteryzują się wysoką wydajnością, ponieważ np. nie pozwalają osiągnąć wymaganej charakterystyki powierzchni.
Zaletą środków rozdzielających zawierających silikon jest ich bardzo wysoka skuteczność rozdzielania. Z kolei ich wadą jest to, że dalsze etapy obróbki odformowanych elementów, np. ich klejenie lub malowanie, mogą być utrudnione, a nawet niemożliwe. Dlatego wymagane są dodatkowe etapy obróbki po formowaniu.
Środki rozdzielające do form stanowią nie tylko barierę fizyczną i/lub chemiczną pozwalającą rozdzielić formowany materiał oraz powierzchnię formy, ale także mają wpływ na charakterystykę procesu, taką jak szybkość spływania formowanego materiału wewnątrz formy, czas cyklu formowania oraz – rzecz jasna – łatwość odformowania. Wybór środka rozdzielającego do form ma też wpływ na wygląd powierzchni odformowanej części, np. poziom połysku, dokładność odwzorowania tekstury, etapy po formowaniu (np. klejenie lub powlekanie formowanej części), a także wpływa na trwałość formy między cyklami jej konserwacji, a także ogólną wydajność produkcji.
Czynnikami, które należy uwzględnić przy wyborze odpowiedniego środka rozdzielającego, są między innymi:
- materiał formy / podłoże
- formowany materiał
- Warunki procesu:
– temperatura
– prędkość linii / czas cyklu
– ciśnienie
– specyfika procesu formowania, czyli np. formowanie wtryskowe, wysokociśnieniowe, napełnianie grawitacyjne formy, tłoczenie itp.
– wahania zmiennych procesu - geometria formy
- etapy dalszej obróbki (powlekanie, klejenie)
- oczekiwany poziom wydajności i produktywność (liczba dobrych części formowanych w danym przedziale czasowym)
- istniejące problemy w procesie (trudności z wypełnianiem wnęk, sklejanie się metali (przywieranie), odpady związane z odformowaniem, wahania warunków procesu itp.)
- oczekiwania dotyczące częstotliwości konserwacji form (czyszczenie)
- wymagania dotyczące wykończenia części (połysk, odporność na zarysowania itp.)
- metoda aplikacji
- względy BHP i ochrony środowiska
Zastosowanie zbyt dużej ilości środka rozdzielającego może utrudnić dalsze etapy procesu obróbki części, ponieważ jej powierzchnia będzie tłusta lub śliska.
Zaleta puszek z aerozolem polega na tym, że zawór natryskowy pozwala zastosować bardzo cienką, równomierną i powtarzalną warstwę. Pozwala to oszczędzać materiał i zapobiegać nadmiernemu dozowaniu. Puszki aerozolowe są też łatwe w obsłudze i elastyczne.
Gromadzenie się środka rozdzielającego, formowanego materiału lub produktów ubocznych i pozostałości po reakcjach chemicznych zachodzących wewnątrz formy (gdy następuje zmiana składu chemicznego tworzywa w procesie formowania) mają negatywny wpływ na wydajność formowania, przenoszenie ciepła, dokładność wymiarową elementów, ich wygląd optyczny oraz wydajność procesu.
Aby zagwarantować odpowiednią jakość elementów, należy regularnie usuwać mechanicznie osady z wnętrza form. Każdorazowo, gdy forma musi zostać oczyszczona na miejscu lub po demontażu, powoduje to utratę mocy produkcyjnych.
Problemy związane z osadami wynikają z dwóch głównych przyczyn:
Nadmiar środka rozdzielającego w formie.
Może to być skutkiem niewłaściwego doboru środka rozdzielającego dla danego zastosowania (np. niekompatybilność z temperaturą procesu) lub aplikacji nadmiernej ilości środka rozdzielającego na formę.
Brak bariery rozdzielającej, co powoduje gromadzenie się formowanego materiału lub produktów ubocznych i osadów powstających podczas procesu formowania.
W takim wypadku możliwe jest, że wybrany środek rozdzielający nie jest odpowiedni dla danych warunków procesu (nieprawidłowa temperatura, nieodpowiednie zwilżanie powierzchni itp.). Przyczyną mogą być także wady procesu aplikacji (niewystarczająca ilość środka rozdzielającego na formie) lub brak odporności fizycznej i/lub chemicznej środka rozdzielającego na materiał, który penetruje warstwę środka i przywiera fizycznie lub chemicznie do formy.
Różne branże przemysłu produkują części z coraz bardziej nietypowych materiałów, aby uzyskać ich lepszą wydajność w coraz trudniejszych warunkach, w jakich stosowane są produkty. Te nietypowe materiały często sprawiają trudności przy formowaniu. Dobrym przykładem jest tu branża samochodowa, gdzie podzespoły silnika (produkowane metodą odlewania) muszą wytrzymywać czynniki chemiczne i fizyczne w coraz bardziej agresywnych warunkach eksploatacji. W wyniku tego produkowane są coraz bardziej innowacyjne, wytrzymałe materiały, a dodatkowo ich wytwarzanie musi przebiegać szybciej, przy jednoczesnym ograniczeniu ilości odpadów. Stanowi to wyzwanie dla producentów środków rozdzielających, ponieważ trudne właściwości chemiczne i fizyczne nowych materiałów sprawiają, że nie są one łatwe w formowaniu i odformowaniu.
Producenci przywiązują też coraz większą wagę do wyglądu części. Często po formowaniu są one poddawane jedynie minimalnym zabiegom końcowym. Przemysł samochodowy wymaga, aby widoczne podzespoły, takie jak kierownice lub deski rozdzielcze, miały bardzo precyzyjne cechy estetyczne (np. tekstura, połysk, odporność na zarysowanie) bezpośrednio po odformowaniu.
W ostatnich latach w wysokociśnieniowym odlewnictwie aluminium dało się zaobserwować coraz większą złożoność form. Coraz częściej stosowana jest metoda odlewania ciśnieniowego, np. High Integrity Casting (Semi-Solid i tłoczenie ciśnieniowe), a także ograniczenie czasów cykli i coraz wyższe temperatury form.
Czynniki te sprawiają, że środki rozdzielające muszą coraz lepiej zapobiegać zlutowywaniu się metali oraz zapewniać odpowiednie smarowanie i odformowanie, aby części produkowane w tych trudnych warunkach miały nadal wysoką jakość. Cele te muszą być osiągane bez negatywnego wpływu na inne cechy wydajnościowe środka rozdzielającego.
Również inne gałęzie przemysłu wymagają coraz bardziej złożonych i skomplikowanych form – w branży produkcji opon mamy z tym do czynienia np. w przypadku opon niskoprofilowych. Formy o takiej konstrukcji sprawiają, że wymagania wobec środków rozdzielających rosną, ponieważ muszą one ułatwiać odformowanie i odpowiedni przepływ gumy. Krytyczne znaczenie ma również wygląd opon po odformowaniu. Wyzwaniem jest więc nie tylko ich odpowiednie oddzielenie od form, ale także osiągnięcie wymaganego efektu estetycznego.
Zakłady produkcyjne wymuszają coraz szersze stosowanie produktów o niskiej zawartości LZO (lotnych związków organicznych), co wynika z regulacji dotyczących BHP i ochrony środowiska. Jest to szczególnie istotne w przypadku procesów wymagających bezpośredniego udziału operatorów, np. w branży produkcji materiałów kompozytowych. Przewiduje się, że tendencja w kierunku produktów coraz bardziej ekologicznych i bezpiecznych w użyciu, będzie się utrzymywać. Będzie to stanowiło bodziec dla producentów środków rozdzielających, aby wytwarzać produkty o takim samym lub wyższym poziomie wydajności, niż aktualnie używane substancje.
Środki rozdzielające dostarczane w pojemnikach zbiorczych najlepiej jest aplikować pistoletem natryskowym lub za pomocą instalacji natryskowej o sterowanych cyklach.
W przypadku produktów aplikowanych inaczej niż z puszki aerozolowej, preferuje się stosowanie wysokiej jakości pistoletów natryskowych lub instalacji natryskowych sterowanych czasowo.